Z-Height Measurement
Z-height measurement, or any measurement
of critical position in one axis, is a common need in many industries.
Many engineers have struggled with trying to get an accurate
measurement of sufficient resolution while coping with design
requirements and implementation problems caused by limited space,
temperature changes, vacuum, target surface interference, and
damage to measurement probes resulting from incidental contact
with the target.
Capacitive and eddy-current noncontact displacement sensors are
becoming a standard technology for these applications because
of their small size, flexibility, ease of use, high resolution,
and robust design. Capacitive and eddy-current sensors can also
be easily customized to fit in specific applications.
Recommended
Equipment
Elite Series Capacitive Sensors
< 1 nm resolution, requires
clean dry environment
|
ECL202 Eddy-Current Sensor
< 100 nm resolution
Works in wet environment
Does not detect nonconductors
|
Technologies
Many
technologies have been applied to these z-height measurements,
each with its own set of challenges. Contact gauging can damage
target surfaces. Optical gauging can suffer from thermal sensitivity,
inconsistent reflectivity of the target material, and may be
difficult to fit in the space required. Some capacitive technologies
can suffer damage to internal electronics if the end of the probe
touches a grounded surface.
Lion Precision capacitive and eddy-current sensors are robust,
thermally compensated, can have resolutions less than one nanometer,
and bandwidths as high as 15 kHz. They can be used in vacuum
and their low power dissipation will not add heat to your sensitive
environment. They can also be customized for a perfect fit. Capacitive
sensors provide the absolute highest resolution but must be used
in a clean environment.
Eddy-Current sensors can be used in wet environments while still
providing resolutions below 100 nm.
Applications
and Industries
Z-Height
measurement is common in industries requiring precise positioning
for optical and nonoptical processing. Some of the many applications
include: semiconductor wafer processing and inspection, microlithography,
optical and nonoptical microscopy, focus and prefocus, mask positioning
and alignment, scanning control, and planarization.
These applications often require critical positioning where nanometers
matter. They also can include challenging environments from slurry
filled environments of chemical-mechanical planarization to the
vacuum environments requiring low outgassing and low power dissipation.
Mask
Alignment
Masks
used in semiconductor processing must be precisely aligned to
achieve today's circuit densities. Four noncontact probes can
be mounted to monitor z-height and parallelism of the mask relative
to the wafer. Maintaining equal outputs from the sensors provides
parallelism while the actual output value indicates the critical
gap dimension.
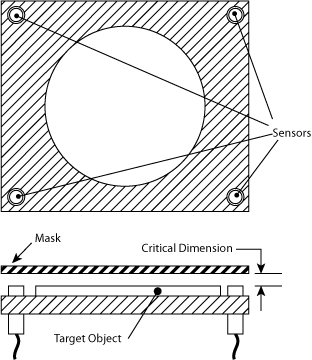
Chemical-Mechanical
Planarization
A precise
lapping process is used in semiconductor, disk drive, and other
industries that require accurately controlled depth of material
removal. The chemical-mechanical planarization process uses an
abrasive slurry on a precision platen that turns against the
object to be lapped. As material is removed, the carrier holding
the object being lapped moves closer to the platen. Eddy-current
sensors do not detect the slurry and thereby provide a precise
measurement of the relative position of the platen to the carrier
(z-height) to determine how much material has been removed. High
resolution of the sensors enable measurements to within 100 nm.
For semiconductor wafers, the eddy-current sensors can "see
through" the wafer and the slurry to measure the distance
to the platen.
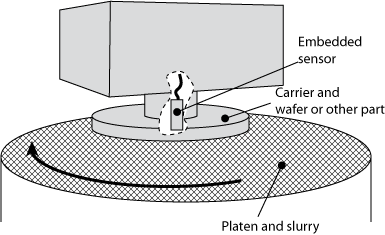
Focus/Prefocus
Optical
and nonoptical microscopy require precise z-height positioning
to maintain proper focus. While optical algorithms exist for
controlling focus, they can be slow while searching for the correct
focus. Noncontact sensors can be used to quickly move to a position
very near the precise focal length where the optical algorithms
can more quickly complete the process.
Because of limited space and extreme demand for performance in
many microscopy applications, there are significant advantages
to using custom designed probes; this drawing shows capacitive
probes configured at 45°.

Scanning
Some
processing and inspection applications use a scanning head to
treat or inspect across the surface of the target object. Z-height
gap and alignment are still critical, but rather than a static
control, this application is dynamic. Lion Precision capacitive
and eddy-current sensors have wide bandwidths of 15 kHz with
bandwidths as high as 80 kHz when required. The fast response
time and excellent phase response enable precise and stable servo
control in dynamic applications.

Article published with
the agreement of Copyright © 2011 Lion Precision.