Tandem Encoders
Tandem
Encoder is new term but one which is increasingly being
used by mechanical and electrical designers. This article explains
what a Tandem Encoder is; how they work; their technical features
and where they are best utilised.
The term tandem
encoder refers to an encoder with at least two measurement
axes but only one power input and one data output. In other words,
two physically independent encoders but with a single electrical
interface.
Tandem encoders
are increasingly being used in those applications with one or
more of the following factors cost pressure, tight space
constraints, weight limits or requirements for high reliability.
For most position
encoders the single largest cost element is their electronics
and the Tandem approach effectively spreads the cost of a single
set of electronics across two (or more) encoders. The result
is that the cost, weight and volume per sensor are reduced.
Another important
factor is the use of slip rings in the host equipment. If slip
rings are being used to energise the encoders, it is often the
case that a tandem encoder is applicable. This is because the
cost, size and complexity of a slip ring are directly proportional
to the number of its contacts. Eradicating slip ring connections
to a second encoder can be a major advantage for the tandem encoder
approach.
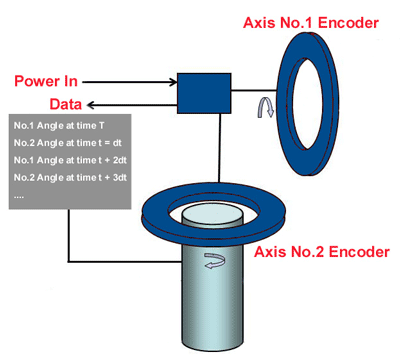
Fig 2
A typical arrangement
for a Tandem Encoder is shown in Fig 2. If we consider the system
as a gimbal mounted camera, we can see that Axis No.1 is the
elevation axis and Axis No.2 is the azimuth axis. Only a single
set of connections to both encoders is required via the slip
ring.
Of course,
not all position sensing technologies are suited to Tandem Encoders.
The Tandem Encoder approach is only applicable when the encoder
electronics can be displaced away from the actual sensing point.
The Tandem Encoder approach cannot be applied if electronics
are required at the sensing point. Optical and magnetic devices
both require electronic devices adjacent to the sensing point.
The Tandem approach is however, suited to capacitive or inductive
sensing technologies, where the electronics required for sensor
operation can be displaced away from the sensing point. Furthermore,
the electronics in capacitive or inductive techniques can be
arranged so that they can be multiplexed across two or more sensors.
Whilst capacitive
devices can be made very accurately, they are best suited to
applications with tightly controlled operating or storage environments
such as offices or laboratories. This is because most capacitive
devices suffer from significant temperature or humidity drift
as well as serious reliability problems if foreign matter
most notably water in the form of condensation or ice
is adjacent to the capacitors plates. Capacitive sensing
devices find it impossible to differentiate between the capacitive
effects caused by water or humidity and the effects caused by
relative displacement of the sensors principal components.
The potential
applications for Tandem Encoders include: CCTV & security
cameras; electro-optic and infrared gimbals; remotely controlled
weapons systems; rotary joints & gimbals; actuator servos
and motor encoders; robotic arms & CNC machine tools; test
& calibration equipment; antenna pointing devices & range
finders; packaging & laboratory automation.
Since most
of these applications involve arduous operating or storage conditions
then it is of little surprise that Tandem encoders have become
mainly associated with inductive techniques. Such techniques
are ideally suited to arrangements where the energisation and
signal processing are carried out remotely from the position
sensing.
Traditionally,
such inductive detectors have used transformer constructions
in the form of accurately wound wire spools. The basic principle
is that as a passive, magnetically permeable element such as
a rotor or a rod moves, it changes the electromagnetic coupling
between at least one primary winding and one or more secondary
windings. The energy that inductively couples in to the secondary
windings is directly proportional to the displacement of the
rod or rotor relative to the primary windings. All windings must
be wound accurately to achieve accurate position measurement
and in order to achieve strong electrical signals, lots of wires
are needed. This makes traditional inductive position sensors
bulky, heavy and expensive.
Traditional
inductive position sensors are usually referred to as resolvers,
synchros, linearly or rotationally variable differential transformers
(LVDTs & RVDTs).
Now there is
a new generation of inductive encoders and these are particularly
suitable to the Tandem Encoder approach. These new generation
inductive encoders uses the same fundamental physics as their
traditional counterparts but rather than the traditional transformer
or wire spool constructions, the new generation use printed circuits
as their main components.
This means
the coils can be produced from etched copper or printed on substrates
such as polyester film, paper, epoxy laminates or ceramic. Such
printed constructions can be made more accurately than windings.
Hence a far greater measurement performance is attainable at
less cost, bulk and weight whilst maintaining the inherent
stability and robustness. The approach also allows the principle
components of the inductive position sensors to be installed
with relatively relaxed tolerances. Not only does this help to
minimise costs of both sensor and host equipment, it also enables
the principle components to be encapsulated. In turn, this enables
the sensors to withstand very harsh local environments such as
long term immersion, extreme shock, vibration or the effects
of explosive gaseous or dust laden environments.
Electromagnetic
noise susceptibility is often cited as a concern by engineers
who are considering next generation inductive position sensors.
The concern is misplaced given that resolvers have been used
for many years within the harsh electromagnetic environments
of motor enclosures for commutation, speed and position control.
The new generation
inductive encoders are produced in either incremental or absolute
forms and output digital data. This means that a Tandem Encoder
can produce a digital data stream with a single data stream carrying
data for both axes.
Article
kindly supplied by Zettlex UK Ltd.
February 2012